Disaster prevention and recovery
What a company can do to prepare for unexpected impacts on its business.
by Phil Shaw

Image © rawpixel.com
The development of complex global supply chains has enabled the footwear industry to offer the customer much greater choice of product, together with significantly lower prices. However, there can be considerable risks to businesses that rely on the production of footwear outsourced to overseas companies often thousands of miles away – that is, increased vulnerability to unexpected disasters and crises.
In recent years, we have experienced a number of disasters which have adversely affected the reliability and stability of these global supply chains. For example, in April 2010, Mount Eyjafjallajökul in Iceland started producing a fine, lightweight, glass-like ash which rose to an altitude of over 8km – an ash cloud that shut down all the European air space for six days. The global economic cost of this event was estimated at £3.8 billion ($4.7 billion).

Boaworm
The global economic cost of Mount Eyjafjallajökul’s eruption in 2010 was estimated at £3.8 billion
The global coronavirus COVID-19 pandemic has put supply chains under tremendous pressure. Recent reports on this developing crisis document how the distribution of goods has been disrupted by factories in China shutting down on a massive scale and transport links being cut to contain the virus.
Man-made problems such as strikes, protests, civil unrest and war can all impact on the availability and movement of products. Of course, disasters can be more localised, affecting only one area or a specific company but the effect of these can be just as serious.
While it is almost certain that no one company can successfully prevent all types of disasters, we can all prepare for the worst. The development of a comprehensive disaster prevention and recovery plan is a vital part of management. This plan should be both dynamic – that is, constantly reviewed and updated to reflect changing circumstances – and accessible to the company personnel who require this information. Some important aspects to be considered when developing these plans in the footwear industry will now be outlined.
Risk assessment
The starting point when developing a disaster recovery plan is to identify the risks. There are many types of risk, and these will be caused either by natural disasters (such as earthquakes or lightning strikes) or by human activity, including strikes, intentional damage, thoughtlessness and loss of concentration. However, although each risk will have its own level of severity, it will also have a likelihood of occurring.
It is the combination of the two factors that will determine how we view, and how we prepare, the appropriate actions to minimise this. Table 1 shows some examples.
Table 1: Possible risks to business continuity | ||
Type of risk | Outcome | Likelihood of occurrence |
Earthquake | Possible death or major injuries | Depending on geographical location |
Lightning strike | Possible injury or loss of power | Rare, but depends on season |
Flood | Damage to property and equipment | Can be highly likely, depending on proximity to rivers/sea |
System hacked | Loss of data and production; possible bad publicity and customer goodwill | Highly likely if communications/IT system is poorly protected or not protected at all |
Road closure | Lack of supplies and deliveries | Often – due to planned infrastructure maintenance, but should be anticipated |
Illness | One or more personnel unavailable; loss of production | Possibly seasonal, or perhaps due to epidemic |
Product failure/recall | customer dissatisfaction and litigation | Financial and reputational loss. Should be avoidable by correct product design and labelling. However, increasingly likely where products are self-selected |
The overall assessment of the risk will determine the potential actions that need to be carried out to minimise the chance of the risk event occurring, together with those actions that will need to take place should the worst happen.
Information is the key
Companies throughout the supply chain regularly exchange information as part of their everyday business activities. Should this information be lost or unavailable due to a disaster, this would lead to profound problems with continuation of the business. Therefore, any plan created to deal with unforeseen problems should recognise the importance of this information – its creation, storage and dissemination. While most companies will have backup copies of some information, this is often stored on-site, and so is as vulnerable as the original data. These copies should be stored well away from the originals – either in a separate, secure location or electronically copied (for example into the cloud).
Cloud storage
Cloud storage is a model of computer data storage in which the digital data is stored in logical pools.
The physical storage spans multiple servers (sometimes in multiple locations), and the physical environment is typically owned and managed by a hosting company. These cloud storage providers are responsible for keeping the data available and accessible, and the physical environment protected and running.
People and organisations buy or lease storage capacity from the providers to store user, organisation, or application data.
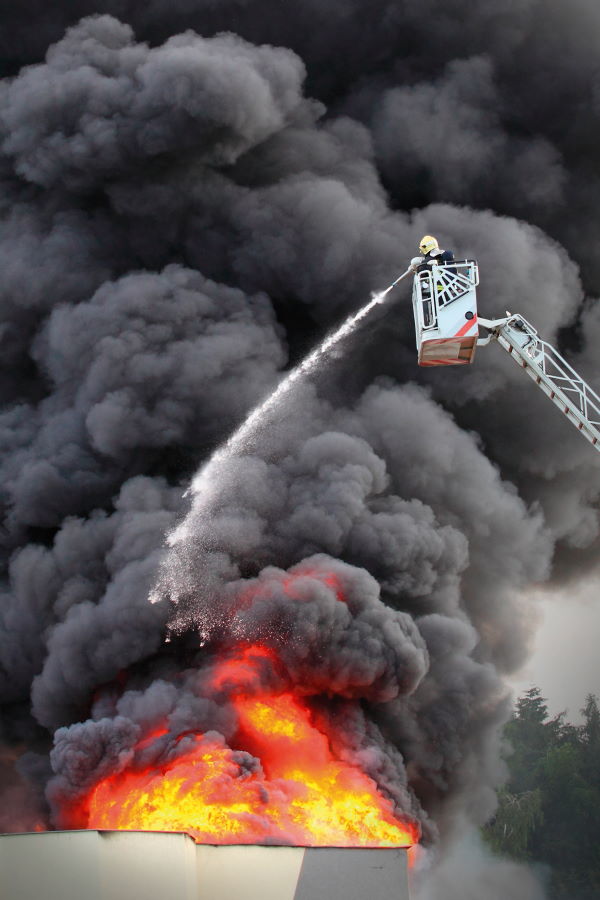
abadonian
Any original information retained on-site should be in a fireproof environment
Where the original information is retained, this should be in a fireproof environment, located away from any risk area (for instance, if the premises are at risk of flooding, the data should be stored on a higher floor).
Should a disaster strike, the people employed within the company will have a major role to play when recreating not only premises and equipment, but also the products, performance statistics and business contacts. Each person within the company will have knowledge of his or her own area of expertise, the products or processes that they regularly work with, and the information they use. Much of this information will be in addition to the core data that most companies regard as essential and protect. Thus, each person will play a vital role in recovering or recreating all of the information that will be needed.
Training
Shoemaking remains a craft-based industry and many of the employees within footwear-producing companies have developed high levels of skill – particularly in terms of product assembly. However, training can also include elements of safety – not only safe working practices, but also how and where members of staff record and maintain their own information so that, if needed after a major problem, they can access this to significantly reduce the time taken to restore the required level of activity.
Employees who have responsibility for maintaining utilities have an important role to play by documenting the location and operation of equipment for regulating and turning off gas, water, compressed air and electricity. In an emergency, it may be important to operate the closing down of these utilities in a specific order to maintain safety, so the information stored should include the relevant protocols.

Employees responsible for maintaining utilities must document how to regulate and turn off gas, water, compressed air and electricity to equipment
In the event of a major problem, there could unfortunately be injuries requiring immediate first aid. The first few moments can often make a major difference to the chances of a recovery or even survival, so having well-trained personnel within the company to provide initial treatment before the emergency services arrive can be vital. Trained first aid personnel should be clearly designated, together with their location and how to contact them, as well as the location of appropriate materials.
The same is true for anyone who has been trained to use firefighting equipment. The location and operation of appropriate equipment such as extinguishers, hoses and fire blankets must be clearly marked, and regular inspection and upgrading/replacing of these should be carried out when necessary.
Product design and labelling
Although unlikely to be as critical to business survival as a major disaster, problems created when customers find that the product fails to perform as expected can still be a significant setback. One dissatisfied customer can be a problem, but often the appropriate response (for example, offering a replacement pair of shoes or a partial refund) can settle this quickly and without too much publicity or loss of goodwill.
However, if the number of products deemed to be inadequate is significant, this may lead to much greater disruption. One worst-case scenario could be that customer complaints reach such a level that local authorities become involved and recall an entire shipment of the products with the attendant media coverage. A high percentage of footwear is transported from the manufacturing origin to the ultimate market place and this can then become a major disaster, as a 20-foot-long container can hold between 2,500 and 5,000 pairs of shoes. Recalling these may involve tracing these through multiple distribution channels and a large number of customers.
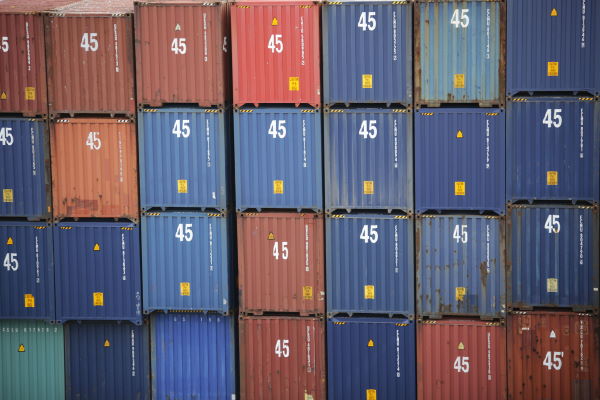
Bernd Dittrich on Unsplash
Recalling thousands of imported shoes may involve tracing these through multiple distribution channels and a large number of customers
The key to preventing this type of problem is careful product design, specification and testing. The current public awareness of environmental issues has certainly sharpened the debate about not only product performance but also the constituent components and materials used in the manufacturing. Therefore, precise labelling of the product, specifying its composition and expected performance in wear, will eliminate most of these types of problems.
Real life teaches us that disasters can occur at any time and come from any source, so it is vital that every company has made adequate preparations to deal with these. A comprehensive and constantly reviewed disaster prevention and recovery plan is not only essential to every company, but also an opportunity to consider current business activities and practices, as well as the level of knowledge available throughout the organisation.
Each person employed will have a role to play in the aftermath of a major disaster. Their knowledge and commitment are key to ensuring that the time taken to recover is as little as possible.
How can we help?
SATRA members are invited to contact the membership team (membership@satra.com) for assistance with preparations for disaster prevention and recovery.
Publishing Data
This article was originally published on page 14 of the May 2020 issue of SATRA Bulletin.
Other articles from this issue ยป