
© SATRA Technology Centre. Reproduction is not permitted in any form without prior written permission from SATRA.

Testing of extreme cold temperature clothing
Clothing designed to provide protection against sub-zero temperatures needs to offer a very high level of insulation.

While the human body can normally regulate both skin and core temperature through reactions such as sweating, it soon loses the ability to keep up with heat loss in extremely cold conditions. Heat flows through the clothing and out into the cold atmosphere. Cold weather protection is largely a question of reducing this outflow of heat to retain body warmth. Normal core body temperature for a healthy human is 37°C, with skin temperature around 34°C. Under low ambient temperatures, we soon begin to feel uncomfortably cold, although core body temperature will initially remain static.
Dangers of heat loss
Any deviation in core body temperature – even by a degree – is serious and causes significant problems for the human body. 'Hypothermia' refers to any condition in which the temperature of the body drops below the level required for normal metabolism and/or bodily function to take place. In humans, core body temperature is maintained at or near a constant level through biologic homeostasis. When the body is exposed to cold, its internal mechanisms may be unable to replenish the heat that is being lost to the surroundings. The result is not just feeling cold – a few degrees drop will severely affect brain function and impair judgement.
Heat loss in extreme cold conditions
Air is a very effective insulator, and many garments rely on trapping a layer of still air to prevent heat loss. Because water is such a good conductor of heat, it is poor at insulating. Moisture will build up inside a garment due to sweating – especially if the wearer is engaged in physical exertion. This can double heat loss through clothing because of the reduced insulation (see figure 1).

Figure 1: Thermal camera images showing how reducing insulation (clothing layers) increases heat loss (red)
Moisture trapped in materials can double the thermal conductivity of the material. The moisture levels may be reduced by using breathable materials or membranes – however, this also adds to heat loss. The moisture will evaporate, and in below-freezing conditions, where the ambient humidity is close to zero, this evaporation will be at a very high rate. While good for keeping dry, large amounts of heat will be lost due to the evaporation process. Heat loss through moisture is compounded by a property commonly known as ‘wind chill’. Moisture loss from the body in still air tends to slow down, as the air surrounding the body becomes saturated and forms a boundary layer. The body relies heavily on this boundary layer of still air to insulate against heat and cold. In fact, many animals have hair or fur to help preserve this layer. Air movement removes this saturated layer, replacing it with dry air, thus increasing evaporation rates. The higher the wind speed, the greater the evaporation rate and heat loss become. At an air temperature of 0°C, a wind speed of 50 km/h will make it feel colder than standing in stationary air at -20°C.
Clothing design
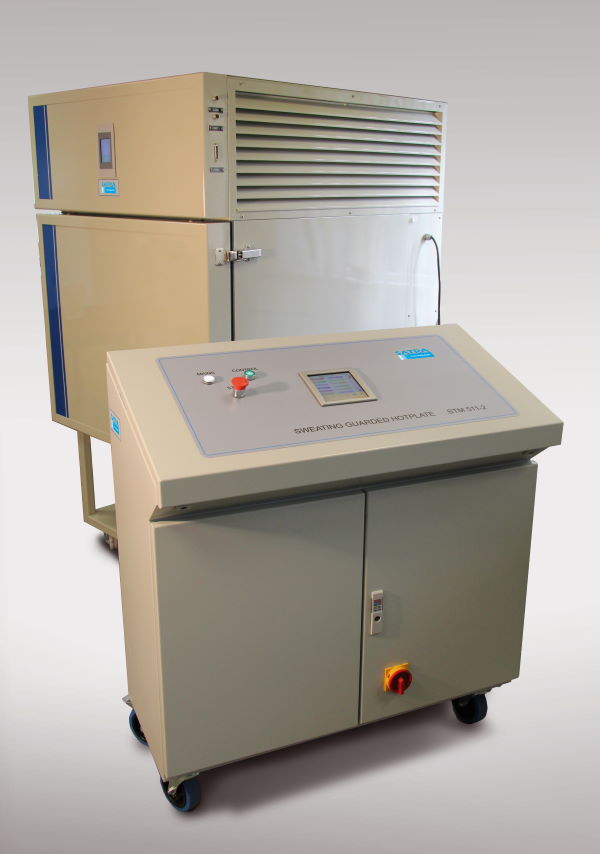
The SATRA STM 511-2 sweating guarded hotplate can be used to determine insulation and water vapour properties of a material
No matter what high-performance materials are used, openings must be provided for the limbs, neck and head. The garment, apart from needing good insulation properties, must trap a layer of air between itself and the body. This layer must be maintained for any garment to function effectively. If this trapped air is allowed to exchange with the air in the environment, no amount of insulation will prevent heat loss. Openings must be carefully designed with effective closures to preserve the trapped air and prevent draughts.
When testing garments designed to protect against cold, it is important to understand the capabilities of the materials involved, as well as the whole garment. Durability is important, and tests such as flex cracking at low temperatures will show the material's suitability. Sophisticated tests utilising SATRA's sweating guarded hotplate should be used to determine both insulation values and water vapour permeability of the materials. Air permeability is also an important property if the garment is designed to be windproof.
Whole garment testing

SATRA’s environmental chamber can be altered from -40°C to +50°C
SATRA has an environmental chamber in which temperature can be altered from -40°C to +50°C and the humidity from 5 per cent to 95 per cent relative humidity (RH) when above freezing. The room is large enough for several people to carry out tasks at different levels of activity. Whole garment testing can be done in two ways. The first method uses a manikin pre-heated to a known temperature – usually 20°C. The manikin is dressed in the test clothing and instrumented with thermocouples so that the ‘skin’ temperature can be monitored. The clothed manikin is then placed in the cold environment and the time taken for the ‘skin’ to cool to a set temperature is measured.
The second method involves using human subjects, monitored both through the measurement of skin temperature (for safety) and questionnaires relating to subject comfort and warmth. This is a very effective way of evaluating the performance of cold weather clothing. Subjects can also carry out a number of different tasks to simulate physical activity. Strenuous activity followed by periods of rest can create conditions that chill the body. The clothing performance in these conditions can be measured only through the use of subjects. Although the manikin does not perspire, it is a useful technique where test conditions raise ethical issues regarding the use of human subjects. SATRA carries out subject-based trials on a regular basis down to -30°C. Colder temperatures require special monitoring and are considered dangerous. The manikin is especially useful where testing involves prolonged periods of extreme cold or where it is simply impossible to use human subjects – for example, when testing children’s clothing.
Advanced testing
Standard laboratory tests are regularly carried out to assess the breathability and permeability of materials. For the sake of control and repeatability, these are conducted at standard laboratory conditions (usually 20°C and 65 per cent RH, or 23°C and 50 per cent RH). However, these laboratory conditions are found only in a few places on Earth, and cannot be said to represent all the climatic conditions in which the materials will be worn in end use.
Fabric technology is constantly improving. A number of innovative 'technical' materials have been developed over the years, with many claiming radical improvements in thermal insulation or moisture management properties. While these products can be tested at standard conditions and may show an advantage over more conventional products, it is likely that their true performance advantages may not be seen until challenged at extreme conditions. As these materials are likely to be more expensive than their conventional counterparts, it is only testing at extreme conditions that will prove why they merit their higher price tag.
SATRA can offer this real-world testing. The SATRA TM376:2009 – 'Advanced moisture management test' method is used to assess whole footwear, and SATRA TM47:2019 – ‘Water vapour permeability and absorption’ is routinely used to assess moisture transmission properties of materials or constructions of materials.
In SATRA TM47, a bath set to 32°C heats pots of known quantities of water. The tops of these pots are sealed by the material to be tested, so that evaporative loss from the water inside the pots must transfer through the material. Periodic mass readings of the pots determine the rate of evaporation through the materials, and from this their permeability is assessed. Water vapour permeability (WVP, mg/cm2·h) is defined by mass decrease (water vapour transfer) through a specimen or construction with a known surface area over a fixed time period.
This SATRA test can be conducted in any ambient (climatic) condition we can create. Any sheet material can be tested in any combination for breathability and moisture absorption, for almost any application on the planet.
Further information on SATRA's PPE certification and testing services is available at www.satra.com/ppe
How can we help?
Please email innovation@satra.com for more information on SATRA’s climatic chamber or the development and/or testing of cold weather products.