The use of recycled materials in footwear
A report on the challenges faced by brand owners and manufacturers wishing to incorporate recycled materials in their new products.

Image © Imgorthand | iStockphoto.com
As a way to make products more sustainable and reduce their environmental footprint, fully-recycled materials or those containing some recycled content are increasingly being used in the manufacture of footwear. The two main benefits of utilising recycled materials are that they eliminate waste and reduce the use of virgin materials. However, there are also challenges that need to be considered, which will be discussed in this article.
What is a recycled material?
A ‘recycled’ material is one that has been reprocessed from reclaimed material through a manufacturing process and made into a final product or a material or component for incorporation into another product. According to BS EN ISO 14021:2016, recycled materials fall into one of two categories – those made from i) pre-consumer waste (any material diverted from the waste stream during manufacturing – for example, cutting waste), or ii) post-consumer waste generated by households or businesses that can no longer be used for its intended purpose, such as plastic bottles that are no longer needed.
It is interesting to note what cannot be classed as ‘recycled’. Rework, regrind or scrap generated in a particular process that can be reclaimed within the same process which produced it cannot be called ‘recycled’. This would include, for instance, polyvinyl chloride (PVC), thermoplastic rubber (TR) or thermoplastic polyurethane (TPU) sprue and flash from the moulding process that could be ground up or cut up and put back into the same moulding process.
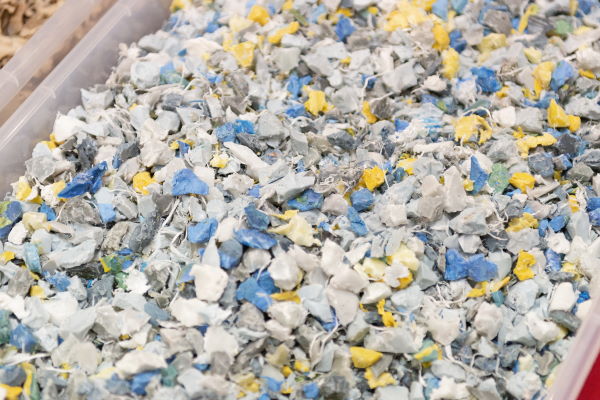
Mikhail Shapovalov | iStockphoto.com
Ground plastic waste prior to reuse
Examples of typical recycled materials
In recent years, a huge number of recycled materials and components have been launched for use in footwear. Recycled plastic waste from sources such as used plastic bottles and recovered ocean plastic has found its way into everything from upper materials and laces to outsoles, box toes (toe puffs) and counters (stiffeners). Insole board is available with recycled content, and even discarded leather scraps are being reprocessed into new upper materials. It is also common practice for shoe boxes and other paper or card packaging items to be at least partially made from recycled materials.
Legislation
How should recycled materials in footwear be labelled and what claims can be made about their use? In the UK, US and Europe, there are no specific guidelines about how to label recycled content or recycled materials used in footwear. The European Union’s footwear labelling requirements state that pictograms must be used to denote the material type(s) in the upper, lining/insole, and outer sole, with options of ‘leather’, ‘coated leather’, ‘textile’ and ‘other materials’. However, there is no change to the labelling, or way to identify through the labelling if, for example, recycled textiles are used.
Nevertheless, the US ‘Guides for the Use of Environmental Marketing Claims’ (16 CFR 260), the UK’s ‘Green Claims Code’ and equivalents in other countries provide guidance about what can or cannot be claimed about a particular product in any supporting documentation or marketing materials.
SATRA recommends the following as a key area for consideration when making claims about the use of recycled materials in footwear products. What is being referred to must be clearly indicated if stating that a product is made from recycled materials or materials containing recycled content. For example, if the main upper material contains 30 per cent of recycled fibres, it would be misleading to claim that the footwear itself is made from recycled materials – or even from 30 per cent recycled materials. It should be obvious in relation to what the claim is being made. Similarly, if a shoebox is made from recycled paper, it should be clear if this information is printed onto the shoebox that it is referring to the shoebox only and not the product as a whole.
Verification of recycled materials
There is an increasing desire from companies to be able to verify that the recycled materials incorporated in their products are actually recycled. This gives confidence in the supply chain, adds credibility to any claims being made, is used to avoid any accusations of ‘greenwashing’ (the making of misleading claims about a product or an organisation’s environmental credentials) and can also be used for differentiation within the marketplace.
SATRA is often asked how a material can be verified as recycled. While some tests to differentiate between virgin and recycled polyester are available, testing alone is unlikely to provide conclusive data for the origin of a polyester and there is no equivalent testing for other materials. The standard route to establish a material’s origins with any certainty is supply chain verification – either independently or via a voluntary standard such as the various schemes available through the Global Recycled Standard or the Forest Stewardship Council.
These schemes will typically use a chain of custody methodology to verify and track materials through the supply chain and a combination of document checks. In some cases, site visits and audits will be used to understand how the waste was generated and if the waste percentages are in line with expected industry averages, in addition to identifying the process into which the waste is going, and investigating what processing was undertaken to turn the waste into an input material.
A further option is the relatively new technology of applying molecular tags with a unique identifier to raw materials, for which traceability can be confirmed as the item passes through the supply chain – for example, tracking recycled polyester through from pellets to fibre to filament and to finished product. It will be interesting to see how this technology develops and to what extent it is adopted in the coming years.
Challenges to be faced
While recycled materials can help to minimise the environmental impact of a product, there are some potential challenges and pitfalls of which a company needs to be aware.
Perhaps the single most important consideration when using recycled materials is to ensure that they are suitable for use in footwear and can consistently achieve the same performance requirements as standard materials. The materials utilised, whatever environmental claims are being made, should be suitable for use in footwear, providing adequate performance, durability and longevity.
Legislation controlling restricted substances in different products is updated frequently. It is therefore vital to ensure that any materials containing recycled content comply with that legislation and that no issues are caused by recycling historical materials containing substances that are no longer permitted, or that are not allowed in the item into which the material is being recycled.
A further consideration is the environmental footprint. In particular, this involves the energy consumed in collecting waste materials, transporting them to a recycling plant (sometimes on the other side of the world) and reprocessing them into new materials. To varying extents, such energy usage will counteract some of the environmental benefits of using recycled materials – the overall footprint that is attributed to a material must be considered, rather than just its recycled credentials.
To have a consistent and reliable supply of recycled materials as an input to the footwear production process, there needs to be a correspondingly consistent and reliable supply of waste going into recycling processes to enable those materials to be manufactured. Logistical challenges related to the COVID pandemic over the last two years have at times hampered the supply chain of this waste. As legislation around the world increasingly restricts or taxes the production of plastic bottles and other single-use plastics, it may become more challenging to secure a supply of certain plastics to recycle into pellets that can, in turn, be used to manufacture footwear materials, including linings and laces.

mirsad sarajlic | iStockphoto.com
Footwear that includes some recycled content could potentially be recycled again
There is also increasing scrutiny being placed on some of the more commonly-used recycled materials such as polyester – for instance, within the EU’s recent communication relating to a strategy for sustainable and circular textiles. Converting plastic bottles into textiles can be considered as ‘downcycling’ rather than recycling, as the process used degrades the quality of the polymer. There is also limited fibre-to-fibre recycling infrastructure available to recycle the resulting material, and it is extremely difficult to recycle a polyester-based material with available technologies if the polyester has been blended with other types of fibre. It is estimated that globally, less than 1 per cent of textile waste is recycled into new textiles.
Finally, the variability of materials used as an input to the recycling process (for example, its colour) can lead to differences in the appearance of the new material being produced, which may not be as uniform or consistent as a traditional material. This needs to be understood throughout the footwear supply chain and ultimately be communicated to consumers to ensure that the materials are not rejected for aesthetic reasons, even if they are not visible in the final product – such as internal components. Such a variation could even be used as a selling point to highlight the ‘environmental credentials’ of the product.
Recycled materials versus recyclability
It is important to note that incorporating recycled materials into a product does not necessarily make it recyclable, and companies choosing to utilise them must be careful to differentiate claims of recycled materials versus recyclability.
Even if individual material or components in finished footwear can be recycled, such a process will not necessarily be viable. The first challenge is the large number of materials or components in a typical footwear item (for instance, leather, plastics, textiles and metals) that for recycling purposes would need to enter different waste streams. It is extremely challenging to separate the footwear down into its constituent parts, which is often complicated further by the use of adhesives for such applications as outsole attachment.
The infrastructure and technology simply do not currently exist at a large enough scale to break down footwear in order to enable each material or component to be recycled or disposed of in the most optimal way. Simpler types of footwear, including moulded plastic sandals, could be recyclable through typical household recycling schemes. However, the recycling facility may not be able to easily identify the materials used, as the footwear may not be marked in the same way as traditional household packaging waste. Hence, the footwear could still be rejected from introduction into that waste stream.
The future
As organisations strive to transition to a circular economy model, finding solutions to convert waste into new materials will become more important. It will also become commonplace for footwear to be designed in order to consider its ‘end-of-life’. This may mean reducing the number of different types of materials used in one shoe, or ensuring that it is easier to disassemble the footwear into its constituent parts for either recycling or waste disposal.
There is already an increase in the number of footwear companies – either alone or collaboratively – developing their own take-back schemes to reprocess finished footwear. If viable, the footwear can be refurbished for resale or, as mentioned earlier, broken down to ensure that each material is passed into the most suitable end-of-life solution.
How can we help?
Please contact eco@satra.com for advice on recycled materials, recyclability credentials of products, and end-of-life solutions for footwear.
Publishing Data
This article was originally published on page 10 of the May 2022 issue of SATRA Bulletin.
Other articles from this issue ยป